AD-IPC-7120
Chassis with front I/O Interfaces for ATX/mATX Motherboard

- With front I/O interface and four to seven expansion slots
- Shockproof drive bay for one 5.25" ODD and two 3.5" HDDs
- LED indicators for power status and HDD activity
- Support four to seven half-size add-on cards
Model | IPC-7120-25D | IPC-7120-35D |
Cooling | ||
Air Filter | Yes | Yes |
Fan | 1 (12 cm / 82 CFM) + 1 (4 cm / 11 CFM) | 1 (12 cm / 82 CFM) + 1 (4 cm / 11 CFM) |
Environment | ||
Operating-Temperature | 0 ~ 45 | 0 ~ 45 |
Non-Operational Temperature | -20 ~ 60° C | -20 ~ 60° C |
Operating Vibration | 1 Grms | 1 Grms |
Non-Operating Vibration | 2 G | 2 G |
Operating Shock | 10 G (with 11 ms duration, half sine wave) | 10 G (with 11 ms duration, half sine wave) |
Physical Characteristics | ||
Weight | 7.01 kg (15.45 lb) | 7.01 kg (15.45 lb) |
Dimensions (W x H x D) | 380 x 164 x 316.5 mm | 380 x 164 x 316.5 mm |
Disk Drive Bay | ||
5.25 External Bay | 1 | 1 |
3.5 External Bay | 1 | 1 |
3.5 Internal Bay | 1 | 1 |
Power Supply | ||
Power Supply | 250W (Single) | 350W (Single) |
Case Study: Vision Positioning Solution for Wafer Cleaning
Background
Wafer cleaning is a crucial part of the semiconductor manufacturing process. The wafer cleaning process removes the photoresist, organic substances, metals, particles, and impurities. It then polishes the wafers using chemical solvents and water, which ensures a precise wafer yield rate.
Wafers are cleaned before and after each process throughout the entire IC production line and takes up approximately 1/3 of the whole production time. In the highly competitive IC wafer production business, precision, efficiency, and optimization are what manufacturers look for.
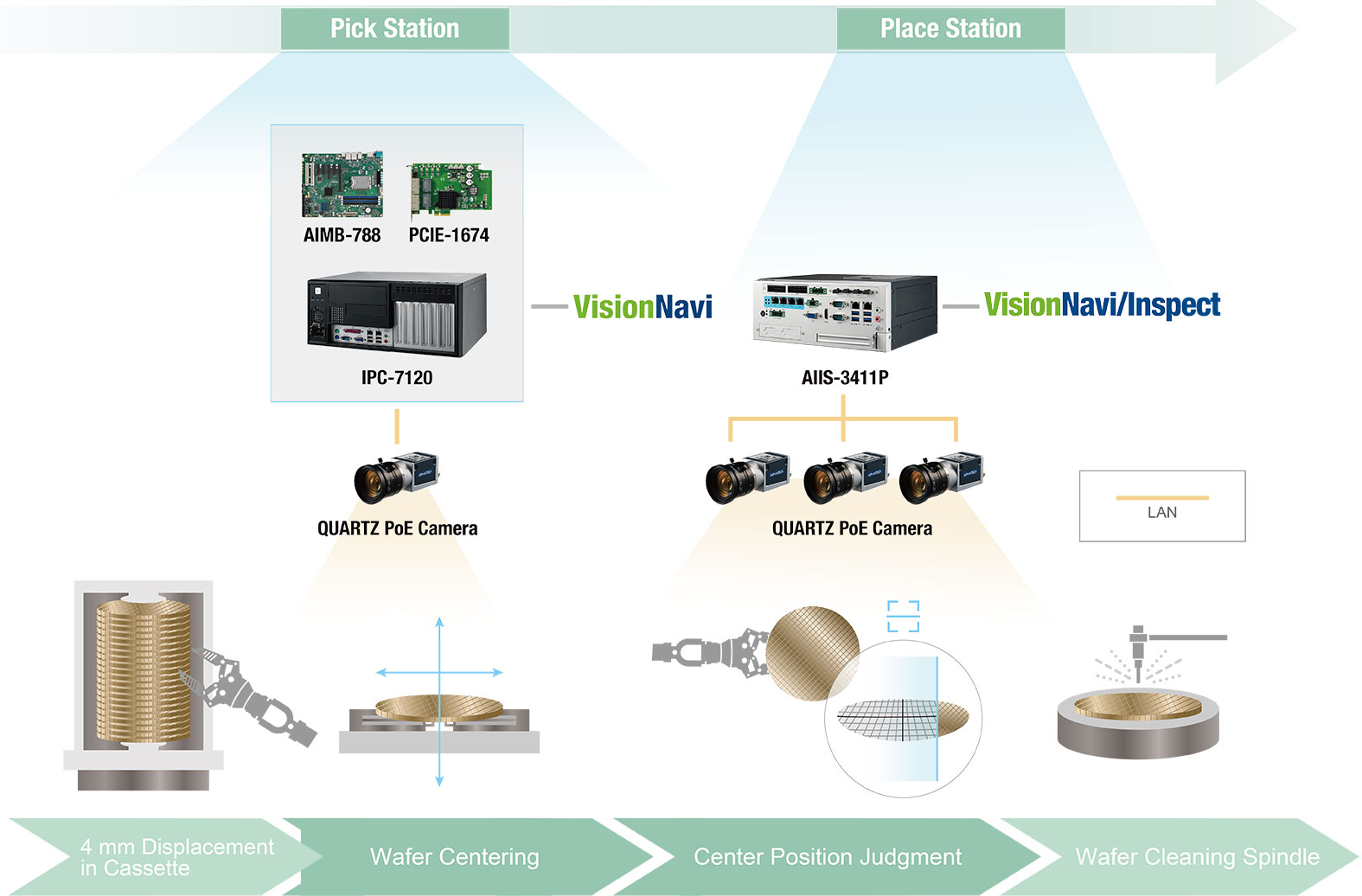
System Requirements
Semiconductor manufacturers were looking for a solution to optimize and shorten wafer cleaning and positioning times. Before the cleaning process there is a step called “wafer centering”, which sits after the wafer is picked up from the cassette.
This is performed by a kind of mechanical gripper device used to re-center each wafer using a positioning algorism. Unfortunately this results in a slight decrease in cleaning efficiency as time is lost when wafers are carefully re-centered. In addition, there’s a small but significant risk of wafer cracking caused by the gripper tool contact, which could result in efficiency loss. Machine vision solution was deployed to replace the mechanical positioning equipment and results show that each wafer can now be accurately re-centered in milliseconds rather than seconds—without wafer damage.
System Description
For this project, the system integrator contractor integrated IPC-7120 + AIMB-787+ PCIE-1674 with built-in VisionNavi and one QCAM mega pixel PoE industrial camera on an intermediate station to help with position correction. The QCAM was installed above the wafer to capture visual data, which is sent back to IPC-7120 + ASMB-787 and VisionNavi for analysis and action.
An AIIS-3411P compact vision system computer is used on the place station with VisionNavi and three QCAMs to judge the center position and any warpage before a wafer is moved to a wafer spindle for cleaning. Once the center position and warpage are calculated, the robot is notified and told to place the wafer onto a cleaning spindle in a precise position without imbalance or vibration to complete the final cleaning process.
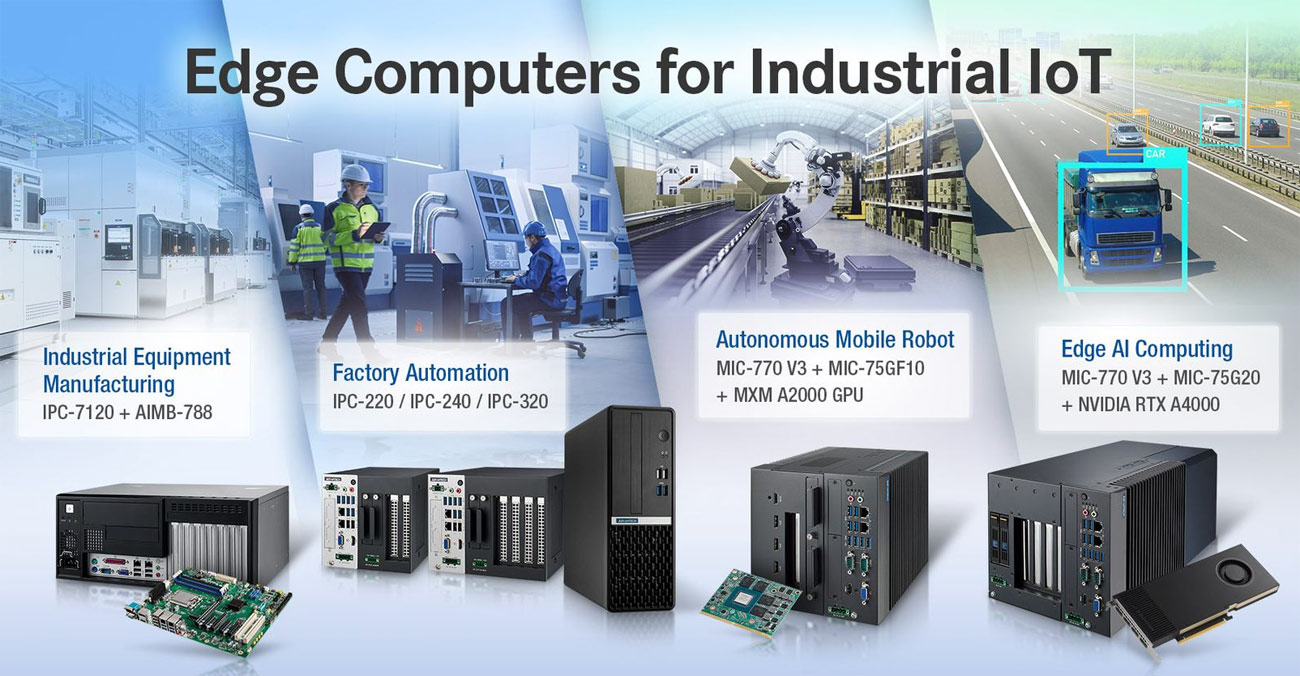